CNC Robotics – Using Robots to Shape Material
Introduction
Advanced Automation and Assembly Ltd are a Sheffield based robotics and automation solutions company focusing mainly on metal finishing and metal cutting solutions, including CNC machine tending and other machine tending operations.
A3L have a strong history in this field offering robust solutions with enhanced support especially where the customer is inexperienced with robotics or finishing automation.
What is Robotic Machining?
Robotic machining is the process of using a 6 axis robot (or any robot) as the mechanism to move a spindle around a tool path to remove material in a similar manner to that of a CNC machine tool. Industrial robots offer large working volumes and full 6 DOF (degrees of freedom) motion and so their use can make a lot of sense. They offer 5 axis cutting over a large volume.
Robots / Accuracy / Stiffness
Articulated arm robots are generally used for robotic machining applications as they have large working volumes and so can really compete favourably on a cost basis with CNC machines with similar working volumes. A robotics system can cost in the order of a few hundred thousand pounds as opposed to 3 to 10 times this amount, for a traditional style machine tool or router. With such a large cost saving why aren’t robotic machining systems more frequently in use?
The answer lies with several interrelated issues but the main two of which are:
- Accuracy
- Stiffness
Accuracy of robots is important on two fronts. Firstly, six axis articulated robots are quite inaccurate. A standard robot with a 100 to 200kg payload and 2-3 m reach will have an accuracy in the order of about plus minus 1 mm, although this figure will change across the robot’s working volume. This is considerably worse than that for a CNC machine. A standard CNC machine will have an accuracy around 50 microns and a router about 200 microns or 0.2mm.
This limits the use of CNC robotics to parts that can be produced leveraging the robots repeatability or to those with lower accuracy and higher manufacturing tolerances. The second area where accuracy comes into play is in programming. Where simple machining operations are called for, accuracy isn’t such an issue because the tool paths can be taught manually. Manual teaching involves moving the robot to a point and saving this point within a program. By saving multiple points a path can be saved which can be later used as a tool path. This teaching method is the traditional way robots are programmed and leverages the robots repeatability. Robots are much more repeatable than accurate with typical repeatability levels being of the order 200 microns compared to an accuracy of approx. 1 mm. Repeatability is the robot’s ability to go back to the same position, whereas accuracy is the ability of the robot to go to a point in space described by a coordinate. Where complex tool paths need to be created manual teaching would take far too long and the robot could be down for days or weeks to generate a program. In these instances, OLP (offline programming) software can be very advantageous. It uses 3D CAD geometry to generate a tool path much more quickly. A path with thousands of points can be generated with the click of a button. However, OLP software relies on accuracy; an accurate model of the robot and tooling, accurate calibration, accurate TCP (Tool Centre Point) etc…
Six axis articulated arm robots are essentially 6 joints in a linear configuration. This makes them flexible. The forces generated by machining metals and other hard or tough materials can lead to deviations from the programmed tool path and further inaccuracy. The stiffness of a robot arm in comparison to the machining requirement is an important factor to take into consideration when selecting a machining system.
Pros and Cons of Robots for material removal
Pros
Articulated arm robots can have a large working volume (the volume the robot can move the end effector around). Applications where a large volume is required should therefore consider a CNC robotic solution. The use of a 7th or 8th axis can also make this volume bigger again. A linear axis can hugely impact the robot’s working volume by extending it sideways by the working length.
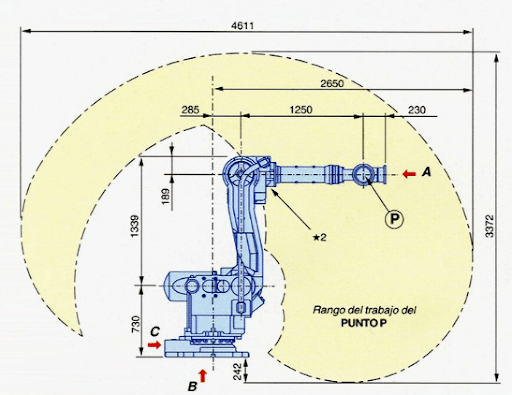
Robotic CNCs can be much cheaper than a machine tool but great needs to be taken to ensure that they can meet your specific job requirements.
A six-axis robot will provide full 5 axis machining capabilities if set up correctly when taken into account along side working volume this really can make a robotic solution a much cheaper than a machine tool solution as 5 axis machines are considerably more expensive than 3 or 4 axis machine. The 6 DOF robot can only provide 5 axis machining as the 6th degree of freedom is lost by the nature of the spindle i.e. the cutter rotates around the z axis as part of the cutting process.
A further advantage is the versatility offered by a robotic platform. As already stated, the robot can have further axes added to increase the working volume but also to provide multiple work areas like pallets on a machine tool. Also there are many tools and technologies that can be added to a robot to change its performance, for example a camera to add accuracy or a force control transducer unit to control the amount of force applied and its direction.
Cons
The stiffness of a 6 axis robot arm is often the major limiting factor. To achieving a well machined accurate part. The lower the cutting forces generated the more likely a robot will be able to deliver. Other means can be used to assist for example jigs to guide the cut or enhancements such as additional encoders on the robot joints to accurately measure the deflections and allow corrective actions to be taken.
There are many ways to improve robot accuracy but its unlikely that a robot will deliver comparable accuracy to a machine tool. Some possibilities are enhanced accuracy robots which are calibrated better by the manufacturer and offer increased accuracy, error correction software which utilises an error map of the robot to modify paths and metrology feedback to mention just a few.
Programming can be very problematic with CNC robotics. Machining tool paths can contain thousands of points and would be very time consuming to tech manually. There are various software solutions out there, but these can be expensive and difficult to setup. However, once setup they can save a lot of time and facilitate the rapid generation of some complex cutting paths. If complex paths are required, then OLP software will be essential.
Applications that suit robots
Trimming panels can be a good application for robotic cutting machines as they generally do not need the accuracy levels of a CNC machine tool and can be quite large. Carbon composite panels or glass reinforced plastic panels are two examples.
Robots are also used for model making in various industries for example making models of cars to assess the design, ergonomics or aerodynamics, or models for film sets. Both these applications are relatively low accuracy and are large volume.
Any low accuracy application such as cutting mould inserts for concrete casting, or machining stone for masonry applications, chamfering or deburring applications, post casting cleanup etc could be considered for a robotic cutting solution.
Low force application similarly are possible. Cutting plastics, foams, soft materials are all possible but also where the process has a reduced force such as waterjet cutting, laser cutting or plasma cutting.
Applications that do not suit robots
Applications that are opposite to the above generally do not suit robot machining systems. High accuracy milling or machining applications would very much more suited to CNC machine tools generally because both he accuracy and the robot stiffness make them unsuitable to achieve part tolerance and react the high machining forces generated in the cutting process.
In application where a machine tool is required then a robot can be used to load and unload parts, change tools and fixtures and other value adding processes. A3L are specialists in this area. See our blog on machine tending for a full introduction into this topic.
Related posts
Robot offline programming
What is offline programming? Robot offline programming (OLP) in essence is the programming of a robo
Belt Grinding Machine Automation
Belt grinding machine automation is used extensively in manufacturing for finishing operations or al
Automated Abrasive Finishing Systems
A3L specialise in delivering robotic and bespoke automated abrasive finishing systems into the UK an