Belt Grinding Machine Automation
Belt grinding machine automation is used extensively in manufacturing for finishing operations or altering the shape of materials. There are many types of abrasive material, but they inevitably have a rough surface that is moved over the part’s surface to remove material and change the surface finish. For example, cast parts can have burrs or rough edges that need to be removed after casting by a belt grinding or fettling process, this involves an abrasive belt being moved at high speed while the cast part is put to it.
Most manufacturers in the UK will have some kind of belt grinding machine or linishing machine on site but these are generally stand-alone machines that are operated by hand. There are very few automated systems where robots are working in unison with belt grinding machines. This is strange when you understand that the belt grinding process is very ‘anti-human.’ It is dangerous, it being a possible cause of many long-term conditions such as vibration white finger (Hand-arm vibration (HAV)), loss of hearing, and several respiratory issues. It is a very dirty process where both part material, and abrasive material, are thrown into the air and lead to a lot of dirt in and around the area, even with a good extraction system. The process can also be mind numbingly dull, workers must stand and manipulate part after part around the grinding belt to complete the work. As a result, this work can be a challenge to recruit for. Workers are difficult to find and then once found, they often leave quickly. Automation can often be the answer. If you have people permanently employed in this type of work, then an automation cell could make a huge difference to your manufacturing processes on many fronts. The shop floor could be made a more hospitable and a nicer place to be (thereby helping to maintain staffing levels), throughput could be increased as robots do not require the breaks that current legislation says workers must have (and this legislation is only likely to get stronger) and quality will become more consistent as every operation will be repeated in the same manner. Clearly there is a strong argument for automating belt grinding and belt fettling processes based on safety but a focus on quality is equally compelling. To understand how automation can aid the quality of belt grinding then we need to focus more on the science of belt grinding. For the remainder of this article, we will dig deeper into this science and how this can affect quality and costs.
The days of traditional sandpaper are over. Companies like 3M & Mirka to name just two have large R&D budgets spent on investigating and developing the latest high-performance abrasive materials. The history and development of sandpaper over the last 200 years is covered well in this article and so we’ll focus on some of the more modern materials; the outcome of these historical developments.
Aluminium Oxide, Zirconia, Silicon Carbide and Ceramic Grain are just some of the more common abrasive materials used for belt grinding. The term Ceramic Grain maybe a little misleading as all the materials are ceramics but generally the term refers to porous aluminium oxide. The porosity is generated in the manufacturing process and aids the grain breakdown under load, as there are other types of aluminium oxide in use, the term Ceramic Grain has become a general reference to a specific type of aluminium oxide.
Friability is the ability of the grains to break up in use. Most modern abrasives breakdown in use to reveal more cutting edges and so elongate their useful life. The Friability of a grain depends on several factors, one major one being the material being finished, or the part, for this reason careful consideration should be taken in choosing the correct abrasive material.
The abrasive backing paper is also a key part of the abrasion process. Generally, there are two main types available in many different thicknesses and weights, these are cloth and paper. The main noticeable difference between backing materials is the flexibility. This can be very significant in the abrasion process and so assuring the right material is important.
Applying the wrong force to a part, can lead to many different undesirable outcomes. To much force may lead to overheating and the burning of the part as well as a premature degradation of the abrasive material. Equally too little force can mean the abrasive grains do not break down which could lead to a short life span and poor-quality abrasion and excessive processing times.
Heat is a physical byproduct of the abrasion process, but it can be a major problem. The applied force needs to be restricted to prevent overheating whilst at the same time enough force is needed to achieve the process requirements. Cooling can be critical. A major cooling variable is the length of abrasive belt. The longer the better as this gives the belt time to cool once through the work zone. This aids abrasive life and cut quality.
By its very nature abrasion removes material and creates debris. This debris can clog and interfere with the abrasion process if it can’t be cleared from the work zone, again this can lead to poor performance and quality problems.
A3L can look at your manufacturing needs and design and build a solution that meets your belt grinding machine requirements. Belt grinding suits automation as it utilises a belt over a contact wheel, because the belt is a consumable the grinding position stays the same (the contact wheel does not wear) whereas with a grinding wheel, the actual wheel reduces in diameter as it wears which means the automation must change the contact point accordingly.
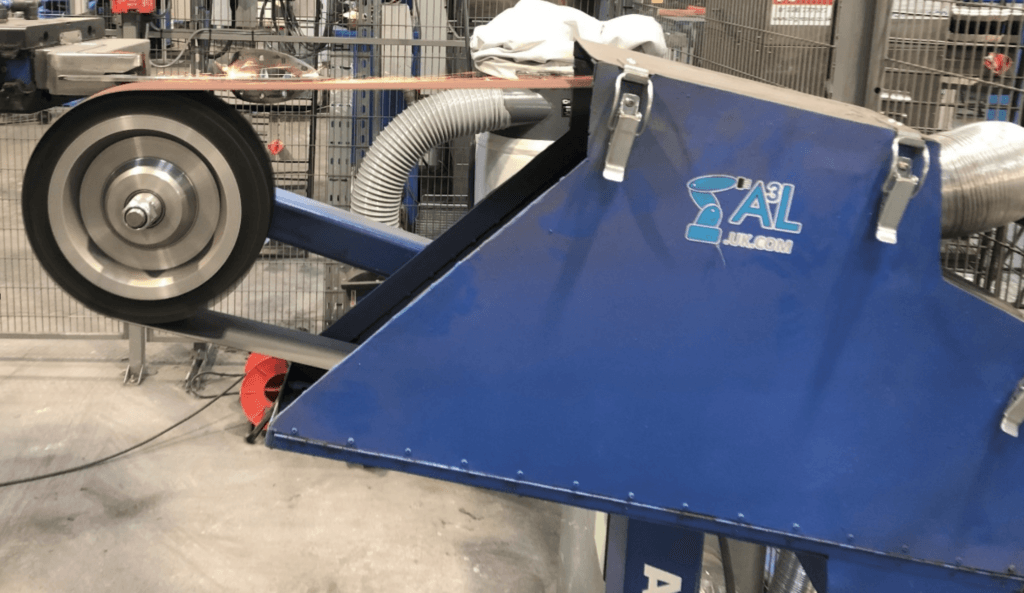
A3L can build bespoke belt grinding machines or offer robotic belt grinding systems. If you are interested in finding out more then please contact us today.
Related posts
Robot offline programming
What is offline programming? Robot offline programming (OLP) in essence is the programming of a robo
Automated Abrasive Finishing Systems
A3L specialise in delivering robotic and bespoke automated abrasive finishing systems into the UK an
Industrial Robotics in the UK
According to the IFR (International Federation of Robotics) the UK was number 24 globally (2021) in